Has the 4th industrial revolution just begun, or has it concluded, propelling us towards Industry 5.0 and beyond?
The 4th Industrial Revolution
The 4th Industrial Revolution, popularized by Klaus Schwab in 2016, heralded a revolutionary era of technologies encompassing cloud computing, the Internet of Things (IoT), data analytics, artificial intelligence (AI), and robotics. However, the term Industry 4.0 or “Industrie 4.0,” with its origins in Germany dating back to 2011, prompts reflection on Bill Gates’s quote, “Most people overestimate what they can achieve in a year and underestimate what they can achieve in 10 years.” Has the 4th industrial revolution just begun, or has it concluded, propelling us towards Industry 5.0 and beyond?
Industrial 3.0
To understand this, we must take a step back and examine the definition of the Industrial 3.0. Traditionally, industrial software applications (HMI, SCADA) were installed on personal computers (PCs) or occasional servers, with scalability contingent on the processing power, memory, and storage capacity of the underlying hardware. Some HMI had dedicated hardware and were not based on PC and Windows operating systems. These applications were not designed to scale beyond the limits of the hardware resources.
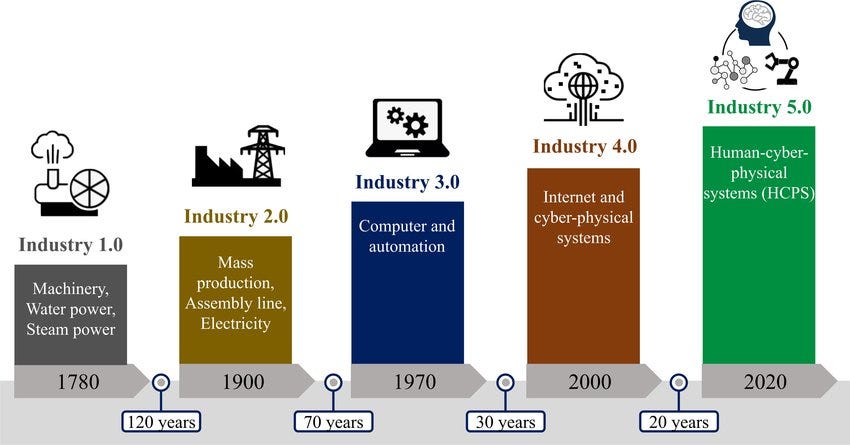
Programmable logic controllers (PLC), responsible for sensing, controlling, and actuating the physical world, were built using dedicated hardware. The real-time requirements of speed, performance, maintenance, safety, and reliability did not align with the event-driven nature of PCs, let alone coping with the impact of the infamous “blue screen of death.”
MOM, MES and ISA95
What changed? The requirements changed. Instead of controlling a machine, there was a need to control a line, a cell, and even a factory. Rather than rearchitecting the level 0, 1, 2 technology stack, existing hardware and software were scaled through replication. Fieldbus networking followed, facilitated by a combination of ethernet-based field bus technologies and data interfaces like OPC and Modbus.
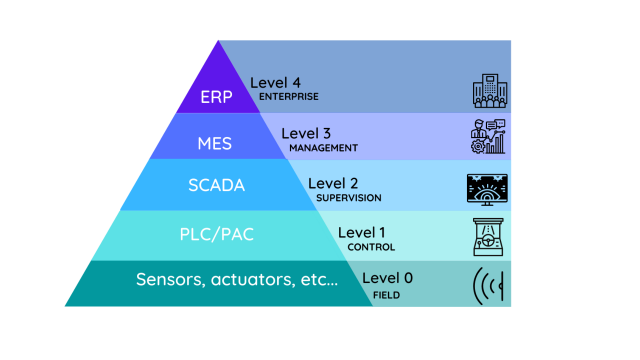
As the system requirements grew manufacturing applications found residence on servers, not confined to server rooms, those were reserved for the IT department. Simultaneously, database and reporting technologies from the IT domain facilitated shop-floor data analysis. In 1995, responding to new Manufacturing Operation (MOM) requirements, ISA 95 attempted to define the functions and data models for level 3. This led to the development of MES applications for production, quality, inventory, and maintenance operations, financed and deployed by IT departments but ‘owned’ by control system teams on the shop floor.
IT/OT convergence
This paradox became known as the IT/OT convergence problem and marked the beginning of the end for Industry 3.0. This application-centric architecture is the predominant architecture of today. However, there are numerous problems with this approach— scaling, performance, maintainability, and usability, all summarized as ‘architectural debt’ or ‘technical debt’. This occurs when the immediate costs of fixing the problem are too high or too difficult to immediately offer a return on investment (ROI). But what is the long term risk to your business?
“We must develop a comprehensive and globally shared view of how technology is affecting our lives and reshaping our economic, social, cultural, and human environments. There has never been a time of greater promise, or greater peril.”
Klaus Schwab, founder of the World Economic Forum
Industry 4.0
The 4th Industrial Revolution is the adoption of Internet technology, including social networks, in the industry domain. The power of these technologies and methodologies has been largely overlooked by many of the large solution providers in the USA and Germany. Ultimately, they have significant investments in existing applications and therefore want the change to happen at their pace and not before they are ready.
Industry 4.0 technologies offer significant advantages over traditional manufacturing IT systems. Envision a Facebook-like platform for the industrial domain, a “MakeBook,” an open marketplace where solvers offer solutions, and seekers purchase services.
Solutions would be instantly available to try, configuring themselves to meet business requirements and constraints. This vision brings us closer to achieving the promise of Industry 4.0 with cyber-physical systems interacting with digital threads, facilitating a seamless exchange of information across the supply chain regarding what to make, when to make it, and what was made.
Conclusion
No, we haven’t achieved Industry 4.0 most business are still delivering Industrial 3.0. However, the dangers of not taking this seriously are real. The journey toward the 4th Industrial Revolution demands a delicate balance between legacy systems and the potential advantages of cutting-edge technologies, emphasized by the necessity for strategic adaptation in the ever-evolving industrial landscape.
“Digital is the main reason just over half of the companies on the Fortune 500 have disappeared since the year 2000.”
Pierre Nanterme, CEO of Accenture
One Comment
Comments are closed.